NEWS
Finger joint wood boards are a widely used product with various applications in interior design and construction materials. It’s constructed from short wood pieces, forming a high-quality finished board. Rubber wood finger joint board is one of the preferred materials, also known for its environmentally friendly characteristics.
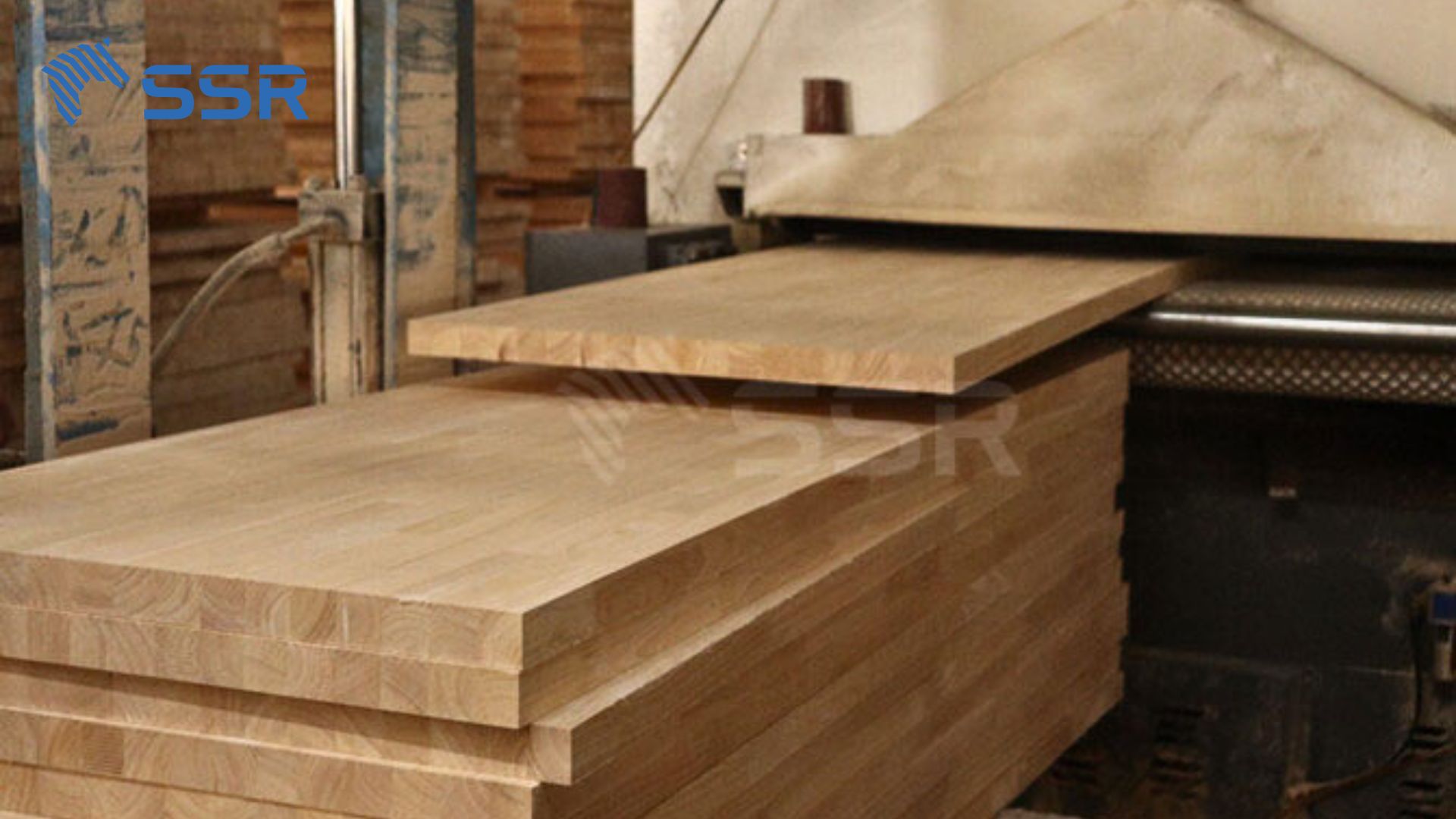
Rubberwood finger joint boards
1. What Rubber Wood Finger Joint Boards Are
Rubberwood finger joint board, also known as a hevea wood finger joint board, is a type of engineered wood product made from rubberwood, derived from the rubber tree (Hevea brasiliensis).
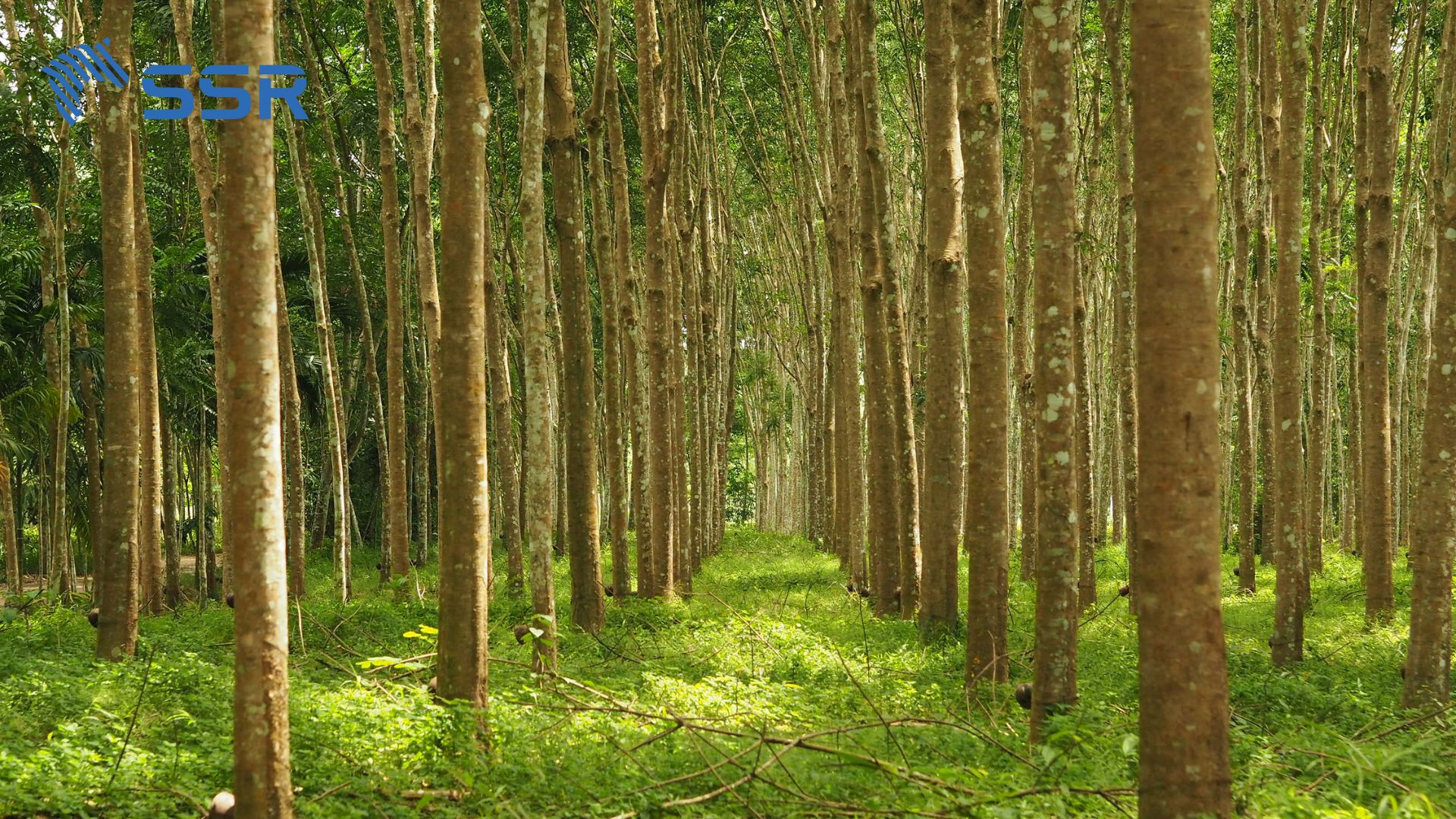
Finger joint boards from plantation rubberwood
These rubberwood panels have vertical and horizontal “finger joint” structures. These are methods of joining wood along the length of the board using tenon joints. Vertical jointing displays the ‘fingers’ on the surface of the board, whereas horizontal jointing reveals the ‘fingers’ on the edge of the board.
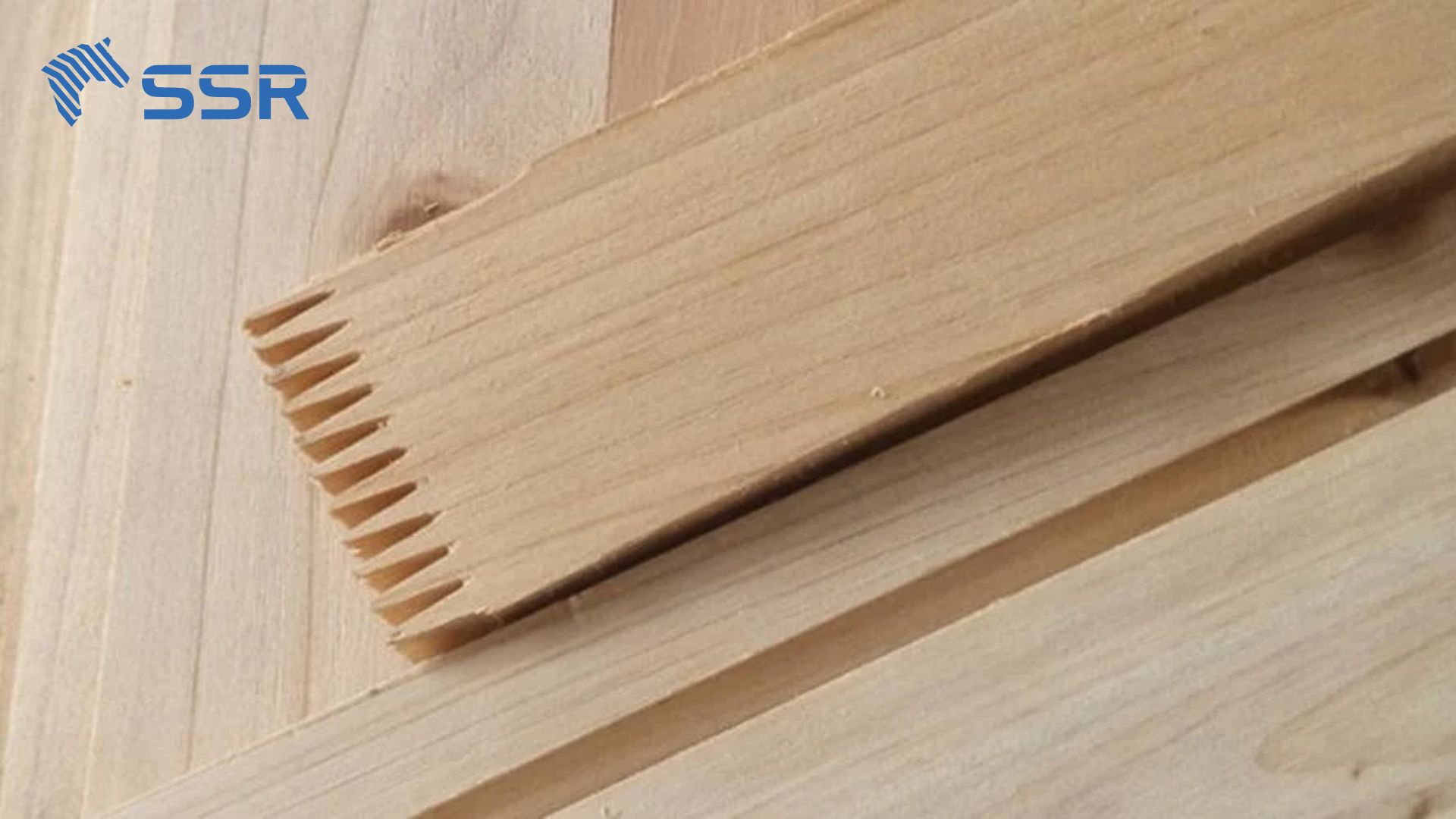
The ‘fingers’ on the edge of the board
Finger joint rubber wood board is a solid rubber wood board made by combining many rubber wooden slats being kiln-dried and termite-treated by the finger joint method into usable lengths strips. These strips are then jointed parallel and pressed with special glues by hydraulic press machines to become the finger joint board.
2. Advantages And Benefits Of Rubber Wood Finger Joint Board
Regarding the physical and mechanical properties of finger joint rubberwood board, It has the following advantages:
- The natural color of the finger joint rubberwood board ranges from medium brown to light brown for the heartwood and light white for the sapwood, providing warmth and a natural look for interior and construction applications.
- Rubberwood has a straight grain, making it easy to work with in various woodworking. It has a uniform or interlocked grain pattern, creating flexibility in design and applications.
- The finger joint rubber board is carefully processed to ensure the quality of finger joints, adhesive, and the density of the hardwood, providing excellent load-bearing capacity and high durability.
- Furthermore, during the production of finger joint boards, the aim is to ensure the stability of the product’s dimensions. Stable dimensions help reduce the risk of warping and twisting in the finger joint board, increasing the durability and applicability of the product.
- The moisture content of the wood board is controlled below 12% to ensure the stability of the product.
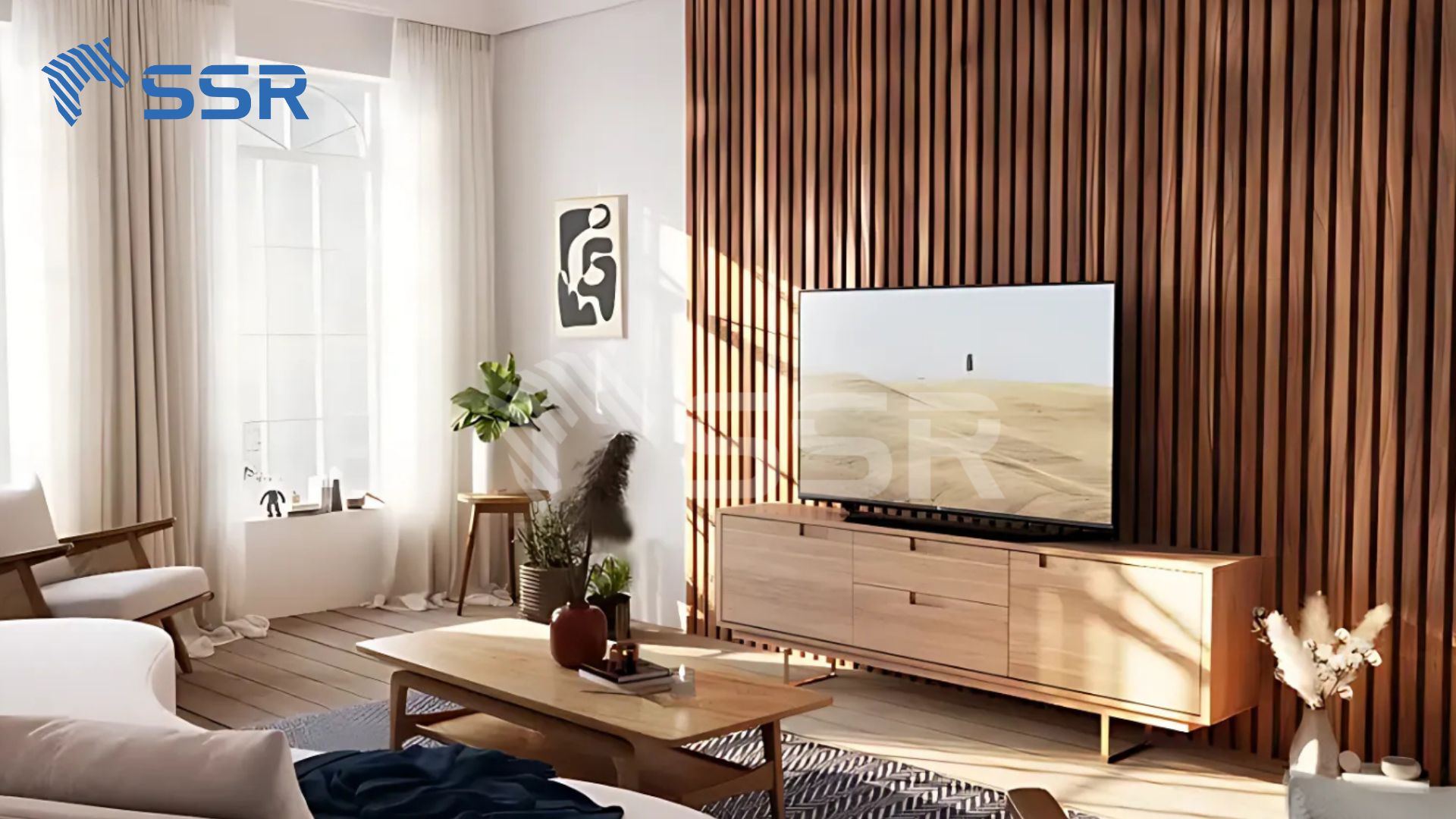
Rubberwood application
- Furniture: Manufacturers commonly use finger joint rubber wood in production furniture such as tables, chairs, cabinets, etc.
- Flooring: The stability and durability of rubberwood finger joint boards enable their application for flooring in residential and commercial spaces.
- Cabinetry: The smooth surface and workability make these boards suitable for cabinetry and kitchen applications.
- Construction: In projects, contractors can utilize rubberwood finger joint boards for paneling, trim work, and various applications requiring a stable and cost-effective material.
Rubberwood finger joint boards offer a combination of sustainability, cost-effectiveness, durability, and versatility, making them popular in the furniture and construction industries.
3. The Manufacturing Process Of Rubberwood Finger Joint Board
The production process for finger joint boards involves several steps, from raw materials to the finished product. Let’s explore the manufacturing process of rubberwood finger joint boards:
Step 1: Raw material
After being harvested, rubberwood is transported to the factory and cut into wood logs.
Step 2: Saw and dry
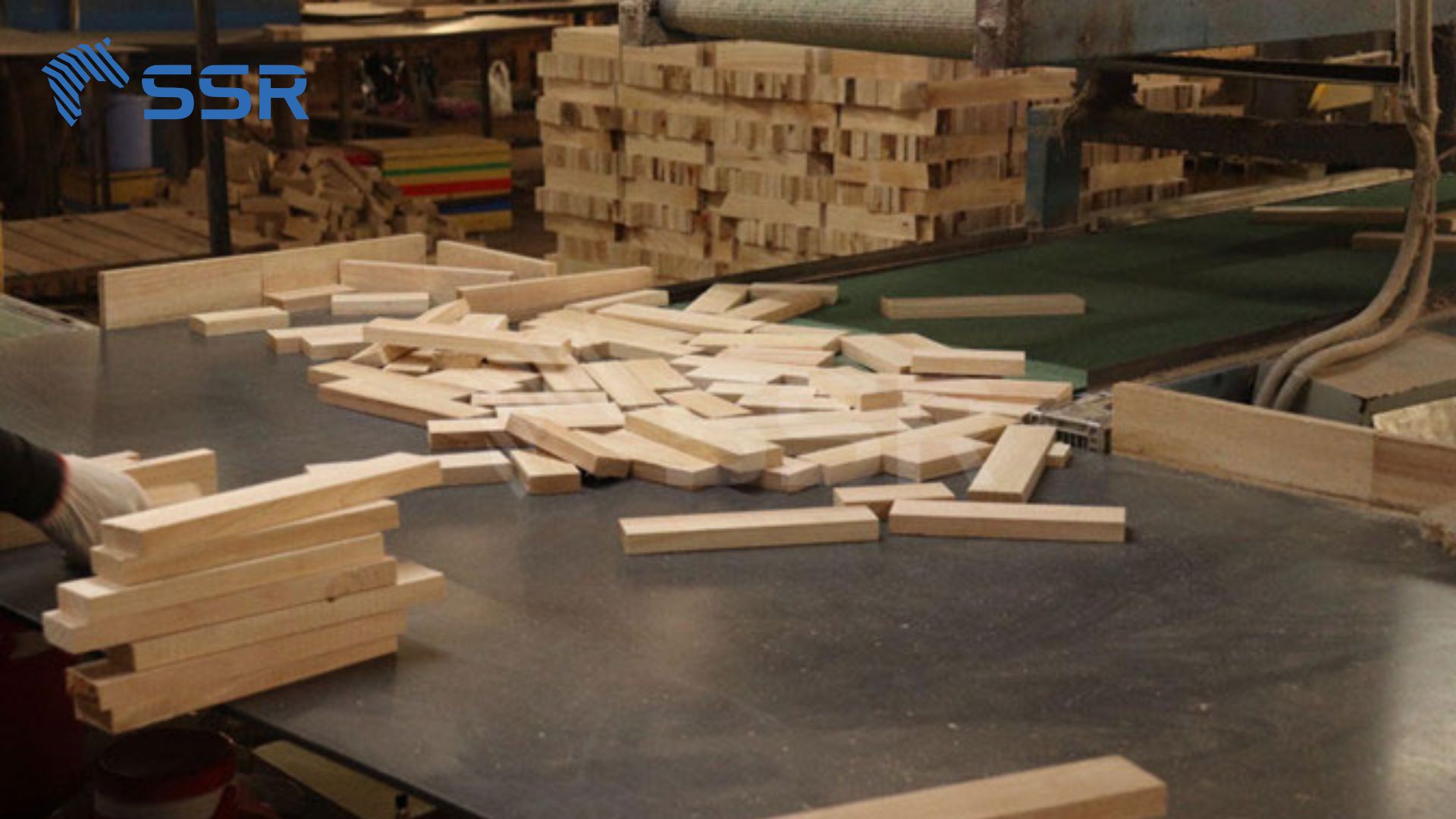
Rubber finger joint board progress
Before grading according to A, B, and C standards, we cut wood logs into smaller slats, kiln-dry, and termite-treat.
Step 3: Making finger joints
Employees grade the uniform wood slats. The next step is creating “finger” tenon joints using a machine, depending on whether they have a vertical or horizontal structure.
Step 4: Gluing
The adhesive is applied to the finger joints to enhance the bonding. A finger jointing machine creates interlocking joints at the ends of the wood pieces.
Step 5: Pressing
The wooden pieces are pressed together in parallel using adhesive and subjected to high pressure from a hydraulic press. Following this, the boards undergo a cooling process.
Step 6: Sanding
The board is sanded to achieve a smooth surface. It’s prepared and ready for the finishing step to enhance aesthetics.
Step 7: Finishing
The finishing of the boards can either conclude at the sanding step or an oil coating to enhance the appearance and protect the wood.
Step 8: Quality control
Quality control is carried out throughout production, ensuring finger joint boards meet specified standards. The final quality control step helps guarantee that the product meets customer requirements.
Step 9: Packing & delivery
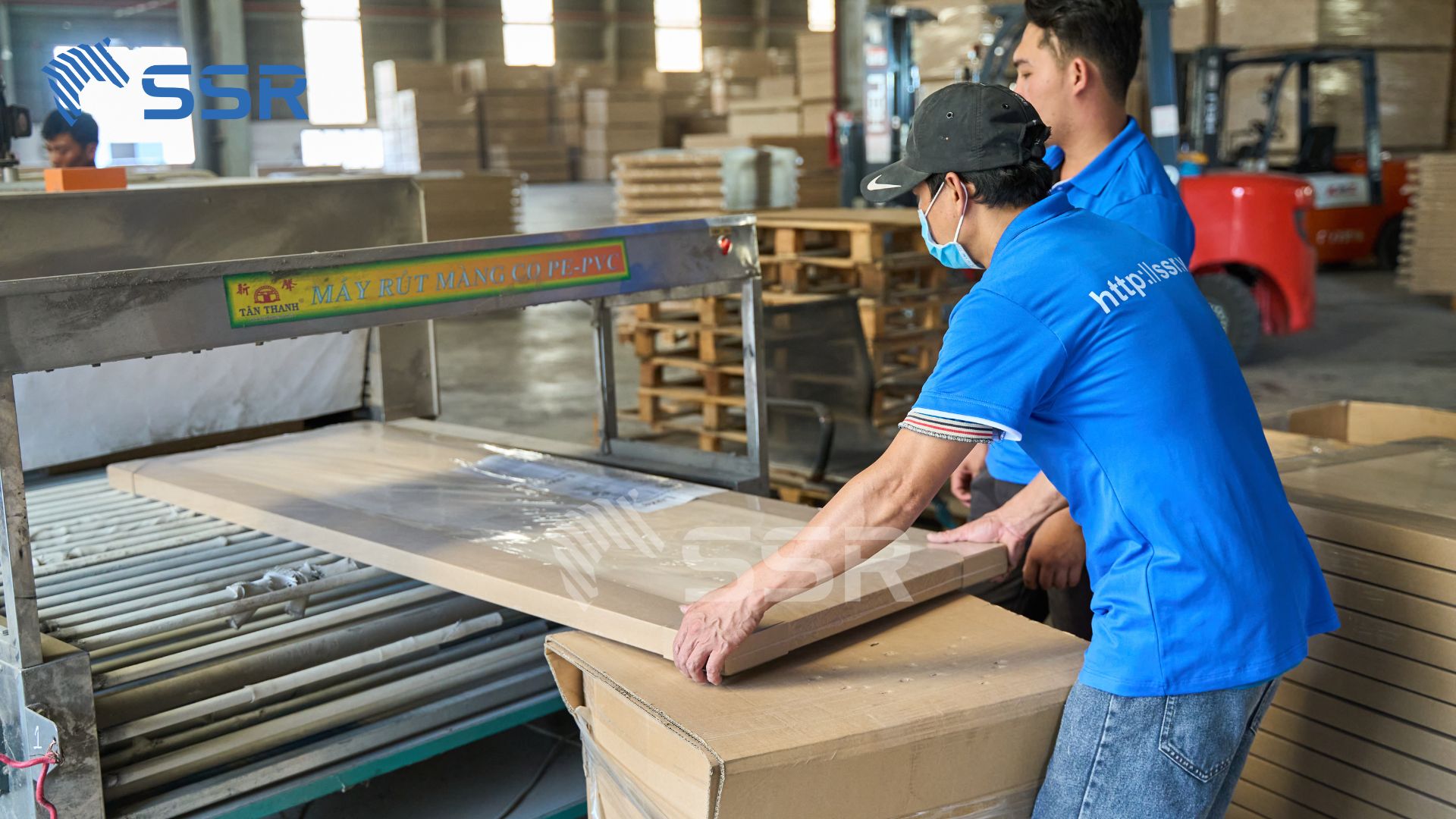
Packaging process
The boards are packaged according to export standards or customer requirements and loaded into containers for delivery.
4. Environmental Sustainability Of Rubberwood (Rubberwood Finger Joint Board)
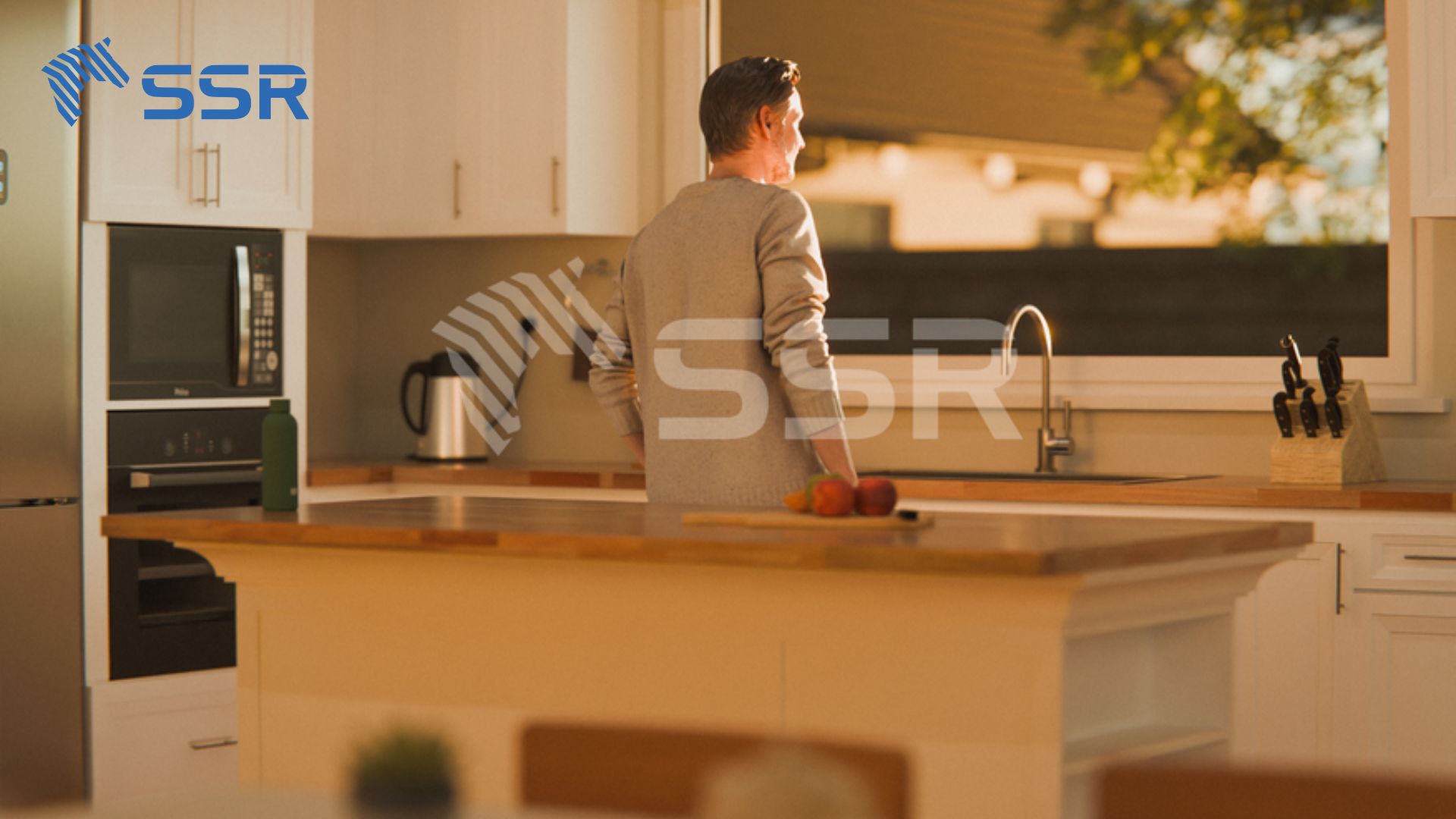
Eco-friendliness of Rubberwood finger joint board
Rubber wood is often celebrated for its eco-friendliness and sustainability, contributing positively to the environment and conservation efforts.
Read More:
Featured Products
Durable Rubberwood Chevron Countertop For Kitchen Tabletop
Specification:
- Wood Species: Rubberwood (Hevea brasiliensis)
- Moisture: <12 %.
- Length & Width Tolerance: 0/+3 millimeters.
- Thickness Tolerance: +/- 0.2 millimeters.
- Glue: D4.
- Surface Finish: Oil coating or sanding 240-320 grit.
- Quality: AA, AC, BC, or customized
- Packing: PE plastic for each piece.
[Good Promotion] Acacia Chevron Countertop Made In Vietnam
Specification:
- Moisture: < 12%
- Stave Length: 150-400 mm
- Stave Width: 20-80 mm
- Length & Width Tolerance: 0/+3 mm
- Thickness Tolerance: +/- 0.2 mm
- Glue: D4
- Quality: AB, AC, BC, or customized
- Surface Finish: Sanding 180-240 grit, both faces.
Top Quality Acacia Edge Glued Countertop Made In Vietnam
Specification:
- Moisture: 8 -12 %
- Stave Length: 150-400 mm
- Stave Width: 20-80 mm
- Length & Width Tolerance: 0/+3 mm
- Thickness Tolerance: +/- 0.2 mm
- Glue: D4
- Quality: ABC, AC, or customized
- Surface Finish: Sanding 180-240 grit, both faces
Featured News
Related News
Crown Moulding for B2B Projects: Installation & Bulk Supply
Crown moulding (cornice) is more than just an architectural detail. It’s a timeless element that bridges wall and ceiling, transforming a room with subtle sophistication. Whether you’re a homeowner looking to elevate your space or a builder seeking premium finishing touches for your next project, crown moulding brings unmatched value in both form and function. In […]

How Many Types of Moulding Trim? An Essential B2B Guide
Moulding trim plays a vital role in interior finishing – bringing together form, function, and refined detail. Whether you’re sourcing materials for large-scale residential projects or customizing high-end commercial interiors, understanding the different types of skirting boards, baseboards, crown moulding, and casing trims is essential. This guide breaks down the most common moulding trim profiles […]
